Overcoming the Obstacles of Industrial Automation Implementation
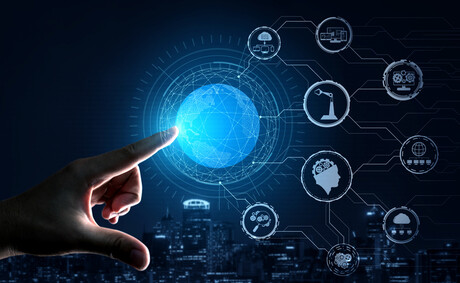
The benefits that can be derived from Industry 4.0 adoption are widely understood. Through this, it will be possible to transform the way in which factory production lines, processing plants and warehouse operations function on a daily basis. In many cases, however, the financial outlay involved is likely to prove problematic. Companies looking to employ such technology will need to do so while keeping the related expenditure to a minimum. The following article will look at how this goal can be achieved.
According to leading analyst consultancy Statista, the worldwide industrial automation market [1] is going to experience substantial growth over the coming years. Having already generated more than $175 billion in revenue during 2020, it is expected to hit the $265 billion mark by 2025 — which equates to a 9% compound annual growth rate (CAGR) over that period. Fortune Business Insights [2] predicts that this 9% CAGR will remain beyond that timeframe, resulting in a total annual worth surpassing $355 billion by 2028.
Advantages of Industry 4.0 and cost implications
Through widespread implementation of Industry 4.0, elevated levels of efficiency will lead to better use of assets and increased output. This in turn means that orders can be fulfilled more quickly to keep pace with customers’ demands. In addition, it will be possible to improve product quality and reduce wastage.
Another aspect of Industry 4.0 that is going to be pivotal is the ability to continuously monitor the key parameters of different items of machinery. This will allow any issues affecting overall performance to be investigated and addressed accordingly. It will support predictive maintenance activities too — so that any component parts that are in need of replacement can be identified before causing costly interruptions in production workflows.
It must be acknowledged, however, that industrial equipment will remain in service for protracted periods of time. Large-scale investments that have already been made mean that such equipment cannot be replaced within a short timeframe. The question therefore is how to get the most out of Industry 4.0 while still keeping the associated costs down.
Before embarking on migration to a smart factory arrangement of some form, the cost implications will need to be fully understood. In situations where there is only limited available budget to fund this work, companies will need an alternative to wholesale replacement of existing machinery. They must therefore look for a means via which they can adequately upgrade it instead.
Modernising connectivity infrastructure
At the foundation of any industrial automation system must be fully effective connectivity. It is through this that all the data will be captured — in order for constituent machinery and processes to be monitored, analysis undertaken and improvements proposed. This connectivity will also be used to execute any necessary actions, should a rapid response be needed to a particular scenario. If it is to work optimally, then a single platform, where everything is using the same communication protocol, is undoubtedly going to be desirable.
Communication can be of either a vertical or a horizontal nature. Vertical communication relies on two-way (duplex) data transmissions between different pieces of equipment and the company’s operation management system. Horizontal communication goes further than this, and generally means that acquired data will be uploaded to the cloud — enabling authorised personnel to access it remotely. This data can then be used to study trends or search for any anomalies that might have a lasting detrimental effect on the industrial site’s operations.
Items of equipment that have already been in operation for a long while will often be dependent on the use of various different field bus protocols, many of which were established decades ago. This presents challenges when they need to interface with back-office enterprise or cloud infrastructure that has been deployed far more recently. If such legacy machinery is to be made compatible with modern industrial automation requirements, it will call for retrofitting connectivity solutions.
Connectivity solutions and the attributes needed
Any hardware that is intended to bring next-generation connectivity to legacy industrial equipment or instrumentation must be straightforward to install, of course. Space constraints may also need to be taken into account. Likewise, it is paramount that this hardware is aligned with the application environment into which it is being placed. It will need to exhibit the robustness necessary for it to cope with the uncompromising working conditions that industrial applications are certain to subject it to. Extreme temperatures, shocks and vibrations, as well as the threat of electro-static discharge (ESD) strikes and potential liquid ingress must all be safeguarded against. Only solutions that have these properties, and can ensure ongoing reliability, should be selected.
Enabling convenient communication between items of equipment supporting different serial interface standards, the Advantech ADAM-4520-F is an RS-232 to RS-422/RS-485 converter module capable of delivering 115.2 Kbps data rates. By attaching one of these units to equipment that was originally fitted with RS-232 interfacing, it is possible to convert the RS-232 signals into isolated RS-422 or RS-485 signals. Through its use, communication distances of up to 1200 m can be supported and as many as 32 different nodes connected. There is no need to change any of the software, thereby facilitating the upgrade process. As well as having 3 kV galvanic isolation, this module has a built-in surge protection mechanism. An operational temperature range of –10°C to 70°C is covered. Supplied in a compact ABS enclosure (with 70 mm x 122 mm x 30 mm dimensions) it can be DIN rail or panel mounted.
Supporting the Modbus TCP protocol, the Brainboxes ED-588 Ethernet gateway allows existing industrial equipment to interact with the enterprise infrastructure further upstream. It offers a robust and intelligent ‘control side’ device that provides the interface to systems on the factory floor environment, commonly referred to as ‘process side’. It has 8 non-isolated digital input and 8 non-isolated digital output channels. The Ethernet port enables data to be transferred at 100 Mbps rates. This DIN rail-mounted unit is supplied in a compact form factor (with dimensions of 101 mm x 128 mm x 22.6 mm), so only takes up minimal cabinet space. These units can be attached to a 24 V supply, and are housed in insulated polyamide casings which are IP20 rated. The gateway may be used to control fans, solenoid valves, reed switches, lamps or motors. In addition, it can deal with data coming in from a multitude of different sensors. There is no software needed, as the unit can be accessed from a web browser. Since it is installed as a COM port on a Windows PC, it has full backward compatibility with older equipment models. Short circuit and ESD protection features are incorporated, as well as over-temperature shutdown. An operational temperature range of –30°C to +80°C is supported.
Conclusion
For a large proportion of industrial operations, there is still a major disjoint between what happens on the factory floor and what takes place at the higher levels. If the advantages of embracing higher degrees of automation are to be fully leveraged, then this needs to change. Through retrofit options, like the ones mentioned in this article, the route towards Industry 4.0 does not actually need to be that complicated or expensive. Through the use of the industrial converter modules and smart sensor plug-ins supplied by TME, it is possible to renovate longstanding industrial operations and start bringing them into the next industrial era.
References
[1] https://www.statista.com/statistics/1219772/industrial-automation-market-size-worldwide/
[2] https://www.fortunebusinessinsights.com/industry-reports/industrial-automation-market-101589
[3] https://www.statista.com/statistics/1101442/iot-number-of-connected-devices-worldwide
[4] https://www.juniperresearch.com/press/industrial-iot-iiot-connections-smart-factories
Power Supplies and BLDC Motor Drivers from Mean Well in TME
Mean Well has launched a new, innovative VFD product series intended for the control and power...
Light and sound signalling systems
Signalling devices are meant to convey unambiguous messages. However, in industrial settings...
Enhancing Efficiency and Sustainability with Motor Control Solutions.
IPD supplies a range of ABB's motor control solutions, which are designed to suit specific...