Safely guiding cables for pick-and-place robots
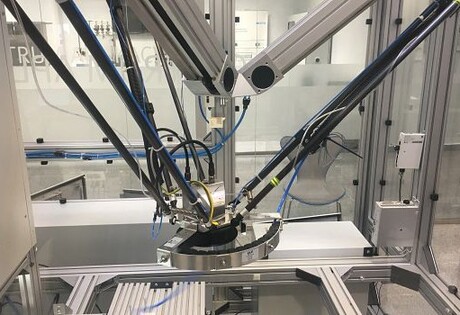
Festo SE & Co. KG is a leading provider of automation solutions for processes and entire production plants. Included in the manufacturer’s product portfolio is the universal parallel robot ‘EXPT’. This pick-and-place robot based on a tripod works with high performance and precision, managing up to 150 picks per minute. Its design and control system enable flexible and cross-application use. This means that a convenient implementation can also be achieved in applications where there are several robots in the production line.
At the lower end of the robot, where the gripper is located, Festo wanted to implement an A5 axis to enable the gripper to rotate quickly and precisely. A special challenge here was the safe and gentle guidance of the cables to the rotating axis. This is because, with continuous operation, a very high number of cycles (360° rotations in less than a second), speeds of up to 7 m/s and accelerations of up to 60 m/s2, there is a heavy load on all cables, which can lead to high wear.
Festo turned to Treotham Automation to help with this problem.
Close collaboration leads to a solution
For the cable guidance, Treotham suggested a rotary energy supply, ie, an energy chain with a reverse bend radius including a rotation module. This would be achieved by running the cables in an energy chain of the E2 micro series. Running in a special rotation module, the energy chain can also achieve the desired high angle of rotation.
The design of this cable guidance provides several advantages for the pick-and-place robot. As the extremely light weight of the guidance allows the robot to be highly flexible and move quickly, the failure rate of the cables leading to the A5 axis has been significantly reduced.
According to Treotham, there has so far not been a solution on the market for this kind of cable feed to rotary axes, which is why the development work involved close collaboration between the Festo engineers and Treotham’s cable specialists.
During this collaboration, specific cables for the application were selected. Among other things, the manufacturer relies on chainflex control cables for high loads in moving applications. In order to save itself the harnessing process, Festo ordered the energy chain as a preassembled ‘readychain’, with the cables drawn in and ready for connection.
Phone: 1300 65 75 64
Bool Ultra Lightweight PPE1 FR Shirt with Segmented Tape
The BW2505T1 Ultra Lightweight PPE1 FR Shirt with Segmented Tape is designed to provide...
Belden GREYHOUND2000 Standard Ethernet Switch
The ruggedised 19″ switch is designed to be future-ready and to evolve as power and...
Mitsubishi Electric FR-D800 series inverters
The inverters are designed to deliver good performance, easy operation and improved energy...