Screened cables with EMC protection in industrial applications
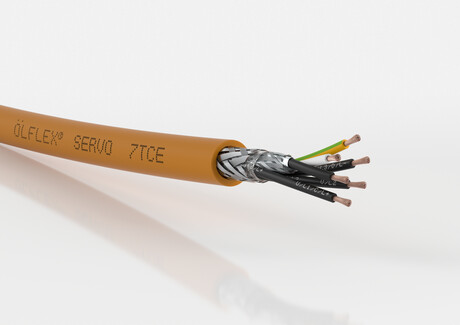
Nowadays it’s difficult to find or create a product or industrial plant without modern cabling technology.
Parts of these processes are managed or controlled by frequency converters, transformers, electrical switches and communication devices.
However, these kinds of switching processes always involve the risk of interference. Precision and the selection of the right components are needed to keep the machine running perfectly.
The aim is for all processes to function smoothly and without errors. This is because something that’s just a bit disruptive like interference on the radio can have far more dramatic consequences in the context of medical technology if the system fails.
This is why industrial environments need ever greater safety against electromagnetic interference: electromagnetic compatibility (EMC).
How does EMC work?
An electromagnetic interference always originates from an interference source. This can be an item of equipment that carries a high current, such as a frequency controlled motor or a cable.
The source of interference corresponds to a disrupted piece of equipment, known as the interference sink. The interference sink can be a sensor or data network cable, for example.
When should screened cables be used?
Wherever electric motors, switches and cables are used for energy transmission, these cause electromagnetic interference. EMI can have a negative influence on data cables, sensors and similar equipment.
In other words, this means that you should rely on power and control cables or data cables with electromagnetic protection through screening in all these areas that are susceptible to interference.
How are screened power and control cables constructed?
There are four different screening types for power and control cables. Three of these shields are particularly suited to use with EMC protection:
- Tin-plated copper braiding. A common method of screening cables is braided copper between the cores and the sheaths. With a degree of coverage of around 80%, the copper braiding forms an effective barrier against electromagnetic fields.
- Copper wire wrapping. For moving cables in robotics, where the screening must withstand torsion, copper wire wrapping is often used. As the copper wires in a wrapping are all positioned parallel to each other, there is no problem with the cable torsion. However, the protection against electromagnetic interference from wrapped cables is often worse as the shield wires do not overlap.
- Aluminium-laminated plastic foil. Individual cores or all cores in the cable can be wrapped with laminated aluminium plastic foil. The plastic foil screening protects your cables and wires, especially at higher frequencies.
How are screened data cables constructed?
Data cables have essentially the same screening as power and control cables, but other abbreviations are common in product designations:
- Tin-plated copper braiding
- Aluminium-laminated plastic foil
There are also two special features for data cables in terms of their screening rating for EMC protection:
- Unscreened. Data transmissions are particularly susceptible to interference, which is why data cables are generally always screened. For certain areas of application for signal transmission, there are unscreened data cables specially marked with the abbreviation “U” (unscreened).
- Twisted Pair. Another design for data cables is twisted pair cables. Individual data pairs are twisted here. The twisting ensures that field effects compensate each other.
How can cables and wires be connected in accordance with EMC?
Did you know that screening has no effect if it is not earthed? The electrical resistance between the cable screen and earth potential must be as low as possible. For this, the contact area must be as large as possible. If the connection between the shield and the EMC component is made correctly and, above all, over as large an area as possible, it generates no or only very low impedances even over long distances. The essential advantage: Your connection is thus particularly electromagnetically compatible.
The requirements at a glance:
- The copper shielding braid is laid out all around (over a large area) and without gaps at the transition into the enclosure.
- The cable gland is connected to the metallic enclosure wall with low impedance.
- The assembly and disassembly of the cable must be possible quickly, easily and without damage to the copper shielding braid.
- Optimum shield contact is ensured at both ends of the cable and applied to the earth potential.
A common method is to apply the shield all around and without gaps, e.g. at the transition from the cable gland to the connector or when introducing the cable into an enclosure by means of an EMC gland.
Only then can the connection act as a Faraday cage and reliably keep out interference signals from outside. It is also important that this optimum shield contacting takes place at both ends of the cable and is connected to the ground potential.
SKINTOP® series cable glands are better suited for flexible cable diameters
LAPP provides these cable glands in two types. Both are characterised by quick and easy assembly and a large clamping range. The cable is centred, fixed, strain relieved and hermetically sealed in a single operation.
The flexible EMC contact spring creates a highly conductive, low-resistance contact with the cable screen in the SKINTOP MS-SC-M (pictured above).
Because the SKINTOP BRUSH series is especially suitable for flexible cable diameters, the products enable you to install them quickly and easily while at the same time providing a high clamping range for your copper shielding braid.
Your benefits at a glance:
- Thousands of ring-shaped brush hairs reliably protect your data streams from induced interference signals from outside.
- A large, variable clamping range makes assembly and disassembly easier and faster.
- The cable is centred, fixed, strain-relieved and hermetically sealed in one step.
Why are connectors important for EMC protection?
Every system is only as good as its weakest point. LAPP connector systems have the advantage of using all the aforementioned screening connection concepts. Very often, EMC cable glands are already integrated into the connector, offer the option of connecting a protective hose and enable the cable screening to be contacted with the working or PE contact of the connector system.
The standard housing is powder-coated with a non-conductive seal between the housing parts, which insulates them from one another. EPIC® EMC connectors offer 360-degree screening and vibration-proof screening connection. The EMC connectors can be identified by their metallically conductive, usually nickel-plated surface. The seals are designed to ensure that the two housing parts pressed or screwed together are in low-resistance contact with metal on metal. The same principle applies to both cable glands and the mounting wall.
Are there pre-assembled power, control and data cables with EMC screening?
Poor EMC is often the cause of installation errors. For a long time, it was customary in industry to buy cables and plugs separately and only connect them when installing them in a machine or production plant, for example.
There are a few disadvantages to greater flexibility: processing quality often leaves a lot to be desired. For instance, if the installer cuts too deep when stripping and damages the core insulation or only partially connects the screening to the housing of the plug, causing EMC problems.
LAPP Australia offers ready-assembled cables, through its Cable Harness Solutions service.
Read the expanded article here: https://lappaustralia.com.au/en/cables-with-emc-protection-in-industrial-applications.
Sealing, securing, simplifying: the role of cable glands in modern industry
LAPP Australia Managing Director Simon Pullinger provides his insights into the role of cable...
The Evolution and Advancement of High-Density Fibre Optic Infrastructure Networks
As the digital era accelerates, the demand for high-density fibre optic infrastructure is rapidly...
WBT's New Ducting Catalogue Is Now Available!
This updated edition offers an expanded range of solutions, expert guidance, and enhanced design...